Diagnose Your Equipment Issues: A Guide to Common Problems in Heavy Equipment
At Nexar Equipment in Nisku, AB, we diagnose and address heavy equipment issues to keep your machinery operational and efficient.
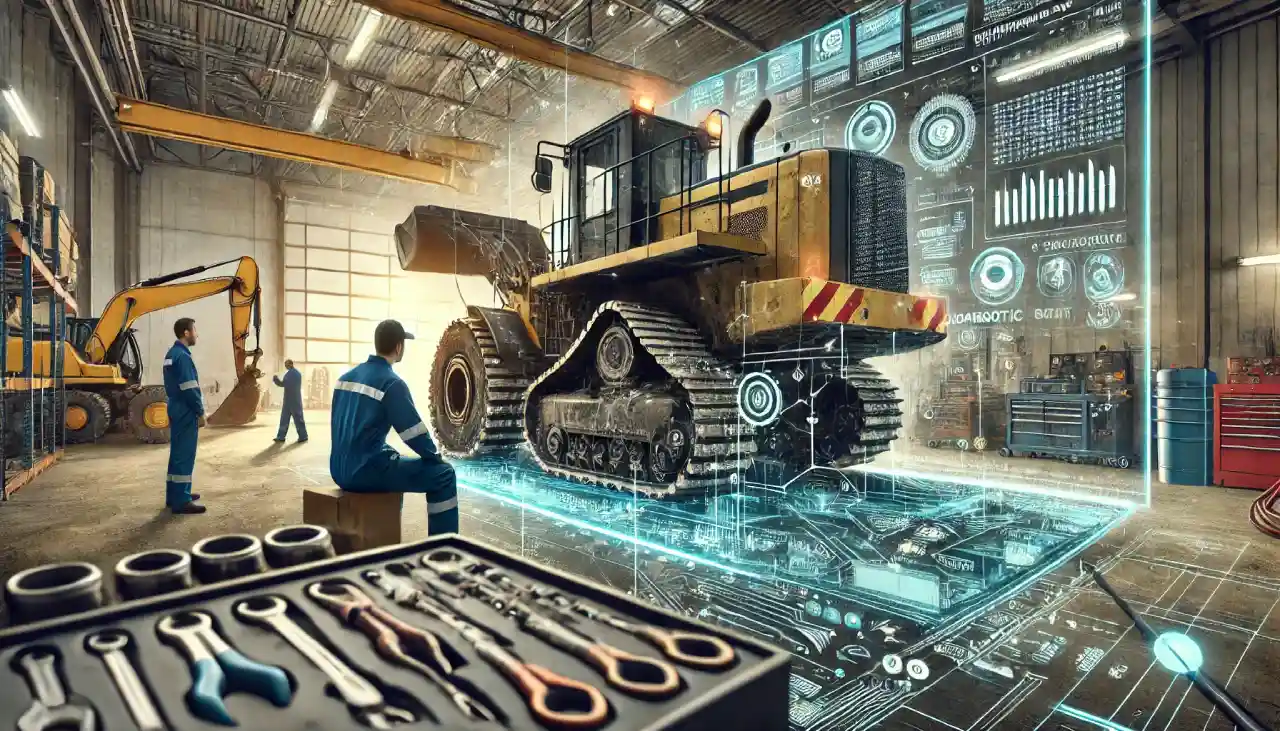
Engine Problems
Overheating
Overheating is a frequent issue in heavy equipment, often caused by factors such as low coolant levels, a malfunctioning thermostat, a clogged radiator, or a failing water pump. At Nexar Equipment, we start by checking coolant levels to ensure the reservoir is adequately filled. Next, we inspect the radiator for any clogs or damage that might obstruct airflow. Our technicians then examine the thermostat, as a stuck thermostat can hinder proper coolant flow. Finally, we test the water pump to ensure it’s functioning correctly and maintaining coolant circulation throughout the system.
Hard Starting
Difficulties in starting the engine can stem from various sources such as fuel system issues, battery problems, or malfunctioning starters. To diagnose these problems, our team begins with a battery check to ensure it has sufficient charge and cleans the terminals if necessary. We then inspect the fuel system by verifying fuel quality and ensuring the fuel filter is clean. Lastly, we examine the starter motor and listen for any unusual sounds that might indicate starter issues.
Hydraulic System Failures
Leaks
Hydraulic leaks are common in heavy equipment and can lead to reduced system efficiency and potential equipment failure. Our diagnosis process starts with a visual inspection to look for oil stains or wet spots around hoses, seals, and connections. We use a hydraulic pressure tester to identify drops in pressure that indicate leaks. Additionally, we inspect the seals, hoses, and fittings for wear and tear to pinpoint the exact location of the leak.
Slow Operation
If your equipment is operating slower than usual, it might be due to hydraulic issues. We start by ensuring the hydraulic fluid is at the correct level, as low fluid levels can impair performance. We check the filter, as a clogged filter can impede fluid flow and reduce operational efficiency. Our team tests the hydraulic pump to ensure it’s operating correctly and maintaining the necessary pressure output.
Electrical System Issues
Battery Problems
A failing battery can cripple heavy equipment, with symptoms including slow cranking and dim lights. To diagnose battery problems, we use a multimeter to check the battery voltage. Our technicians clean any corrosion from the battery terminals and connectors. Additionally, we perform a load test to assess the battery’s performance under operational conditions and ensure it can sustain a charge.
Alternator Failures
The alternator charges the battery and powers electrical systems in heavy equipment. To diagnose alternator issues, we start by testing the alternator’s output voltage with a multimeter. We inspect the drive belt for wear or slippage, as a faulty belt can affect the alternator’s performance. Finally, we check for dashboard warning lights indicating problems with the charging system.
Transmission Issues
Slipping
Transmission slipping can be a sign of serious issues in heavy equipment. To diagnose transmission slipping, our team first checks the transmission fluid level and condition, as low or dirty fluid can cause slipping. We inspect the clutch for signs of wear if the equipment uses a manual transmission. We also conduct pressure tests on the transmission to identify internal leaks or pressure drops that might be causing the problem.
Noise and Vibration
Unusual noises and vibrations often signal transmission problems. To diagnose these issues, we start by examining the transmission fluid for metal shavings or contaminants, which can indicate internal damage. We check the transmission mounts for wear or damage, as faulty mounts can cause vibrations. Our technicians listen for grinding or clunking sounds during operation, as these noises often indicate gear issues.
Brake System Problems
Insufficient Braking Power
If the brakes aren’t performing as expected, it could be due to several issues. We start by ensuring the brake fluid is at the correct level. Our team inspects the brake pads for wear and replaces them if necessary. Additionally, we bleed the brake lines to remove any trapped air that might be reducing braking efficiency.
Noisy Brakes
Squealing or grinding brakes indicate issues that need immediate attention. To diagnose noisy brakes, we check the condition of the brake pads for wear or glazing. We inspect the rotors for grooves or warping, as damaged rotors can cause noise. We also ensure there is no oil or grease on the brake components, as contamination can also lead to noisy brakes.
Undercarriage Problems
Track and Tire Wear
Heavy equipment tracks and tires endure significant stress and wear. To diagnose track and tire wear, our team starts with a visual inspection to look for signs of damage such as cracks, cuts, or uneven wear patterns. We ensure the tracks are properly tensioned to avoid excessive wear. We also check tire or track alignment to prevent uneven wear and extend their lifespan.
Suspension Issues
A faulty suspension can lead to poor handling and operator discomfort. To diagnose suspension issues, we inspect the shock absorbers for leaks or damage. We check the springs for cracks or breaks, as damaged springs can affect the suspension’s performance. Our technicians examine the suspension bushings for wear or deterioration, as worn bushings can lead to instability.
Steering Problems
Hard Steering
Difficulty in steering can be due to several factors. We start by ensuring the steering hydraulic fluid is at the proper level. We test the steering pump to ensure it’s providing adequate pressure output. Our team inspects the steering linkage for damage or wear that might be causing hard steering.
Steering Wander
If the equipment tends to wander or pull to one side, it might be due to alignment issues. We check for proper wheel or track alignment to ensure the equipment travels straight. We ensure the tires are inflated to the recommended pressure, as low tire pressure can affect steering. We also inspect suspension components for excessive wear, as worn parts can cause steering instability.
Preventative Maintenance Tips
Regular inspections and maintenance are crucial for keeping heavy equipment in optimal working condition. At Nexar Equipment, we conduct thorough inspections of all components regularly and adhere to the manufacturer’s service schedule for maintenance and part replacements. We keep components clean to prevent dirt and debris from causing damage and ensure operators are trained to recognize early signs of problems and report them promptly.
Conclusion
Diagnosing equipment issues in heavy machinery requires a systematic approach and attention to detail. At Nexar Equipment, we understand that recognizing common problems and their symptoms can significantly reduce downtime and extend the life of your equipment. Regular maintenance, timely repairs, and vigilant monitoring are essential practices for keeping your heavy equipment in optimal working condition. By following this guide, operators and technicians can effectively diagnose and address issues, ensuring the smooth and efficient operation of their machinery. Trust Nexar Equipment to keep your heavy equipment running at peak performance.
Contact Us
Get in touch with Nexar Equipment today for more information or to schedule service!